The condition of a pavement is assessed by raising parameters that allow users to measure comfort and safety, ensuring trafficability at any time of the year and in different climatic conditions. In order to assist consultants and designers in their decision making through the collection of field data, we have equipment and trained technical staff capable of meeting market demands. Thus, we can mention the main field surveys:
STRUCTURAL EVALUATION OF ASPHALT FLOORS
Non-destructive assessment equipment
The equipment used in non-destructive assessment by Stratura Asfaltos are:
- Impact loading: Falling Weight Deflectometer (FWD);
- Quasi-static loading: Benkelman Beam Deflection Test (BBD).
1. FWD – Falling Weight Deflectometer
For structural evaluation of the pavement, we consider the maximum deflections recoverable by means of an impact deflectometer commonly known only as FWD. Briefly, the operation of the FWD is characterized by the use of dynamic loading, where a set of masses in free fall collides with a rubber damping system (buffers), transmitting the force from this impact to a segmented circular plate ( radius of 15cm), which is in contact with the pavement. Through a pressure transducer connected to the circular plate response system, the applied load is registered. From there, the recoverable deflections are measured by means of deflection sensors (seismometers) positioned at a known distance along a crossbar.
2. Benkelman Beam Deflection Test – BBD
For structural evaluation of the pavement, we also have the Benkelman beam, which is essentially composed of a fixed part and a movable beam.
The fixed part is supported on the floor by means of three adjustable supports, the mobile beam being coupled to it by means of a joint, with one end (probe) in contact with the floor, and the other end activating an extensometer with 10-2 mm accuracy.
It is equipped with a vibrator, which has the function of overcoming friction between moving parts and avoiding any inhibition of the extensometer needle.
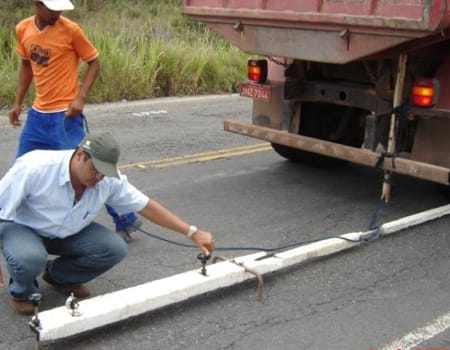
FUNCTIONAL EVALUATION OF ASPHALT FLOORS
The friction characteristics through the tire-pavement grip on highways and airports play an important role with regard to safety and comfort for users.
1. British Pendulum Test (Microtexture)
British Pendulum Test (microtexture), aims to perform a wet skid resistance test. Measurement of the friction coefficient using the Pêndulo Britânico.
The friction created between the tire of a modal and the pavement is responsible for maintaining the direction of a vehicle on the highway, which is strongly interfered by weather conditions, mainly from rain and excess moisture on the pavement surface. The presence of water on the surface of the pavement, in contact with the tire, causes hydrodynamic pressures to be generated in the tire / pavement contact zone and, depending on the amount of water and the speed of the vehicle, the phenomenon of hydroplaning can occur, which is the lack of grip between the tire and the surface of the road making it impossible to perform any maneuver requested by the driver.
The friction between the surfaces must be understood as the sum of two parts. One is related to adhesion at the points of contact between the two surfaces, final contact between exposed aggregates and the tires. The second portion appears if the irregularities in one of the surfaces produce deformations in the other in order to change its original shape.
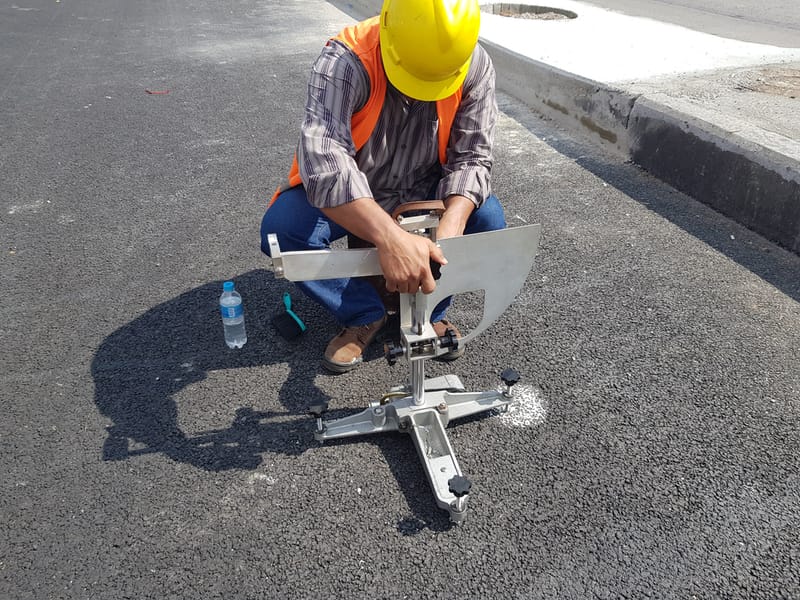
2. IRI – Internacional Roughness Index
Inertial Laser Profilometer:
Initially, conditions or comfort levels are assessed by measuring the irregularity of the road. By definition, irregularity is the deviation of the track surface from a reference plane (true flat surface), which affects vehicle dynamics and rolling quality.
The International Roughness Index (IRI) it consists of a rectified average of the computed variations of the absolute profile, being representative of the vertical movements induced to the vehicles by a frequency band perceived both in the responses of the vehicles and in the comfort felt by its occupants. The IRI measurement scale is dimensionless and uses a factor equal to 1,000, and can therefore be represented in m / km.
3. Sand Patch Method (Macrotexture)
The macrotexture treats the surface roughness of the pavement imposed by the bulge caused by the aggregate.
It is related to friction at speeds above 50km / h; the ability of the pavement to drain surface water, avoiding the phenomenon of hydroplaning; spray formation; the formation of the night mirror; tire wear and excessive noise levels.
The granulometric distribution, the characteristics of the aggregates (shape, size, etc.), the dosage of the mixture and the construction process greatly influence the final macro-texture of the floor. The most widespread way of measuring macrotexture is through the sand stain (or height) test standardized by ASTM D965-15.
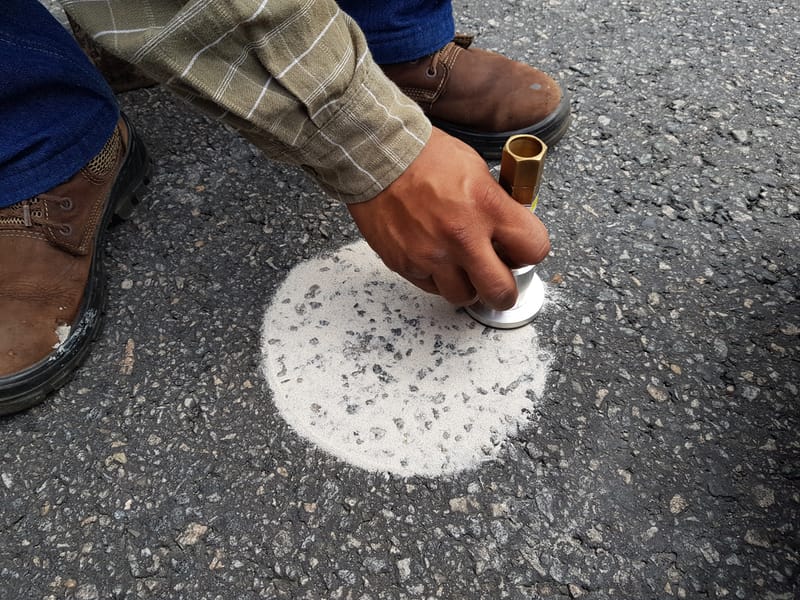